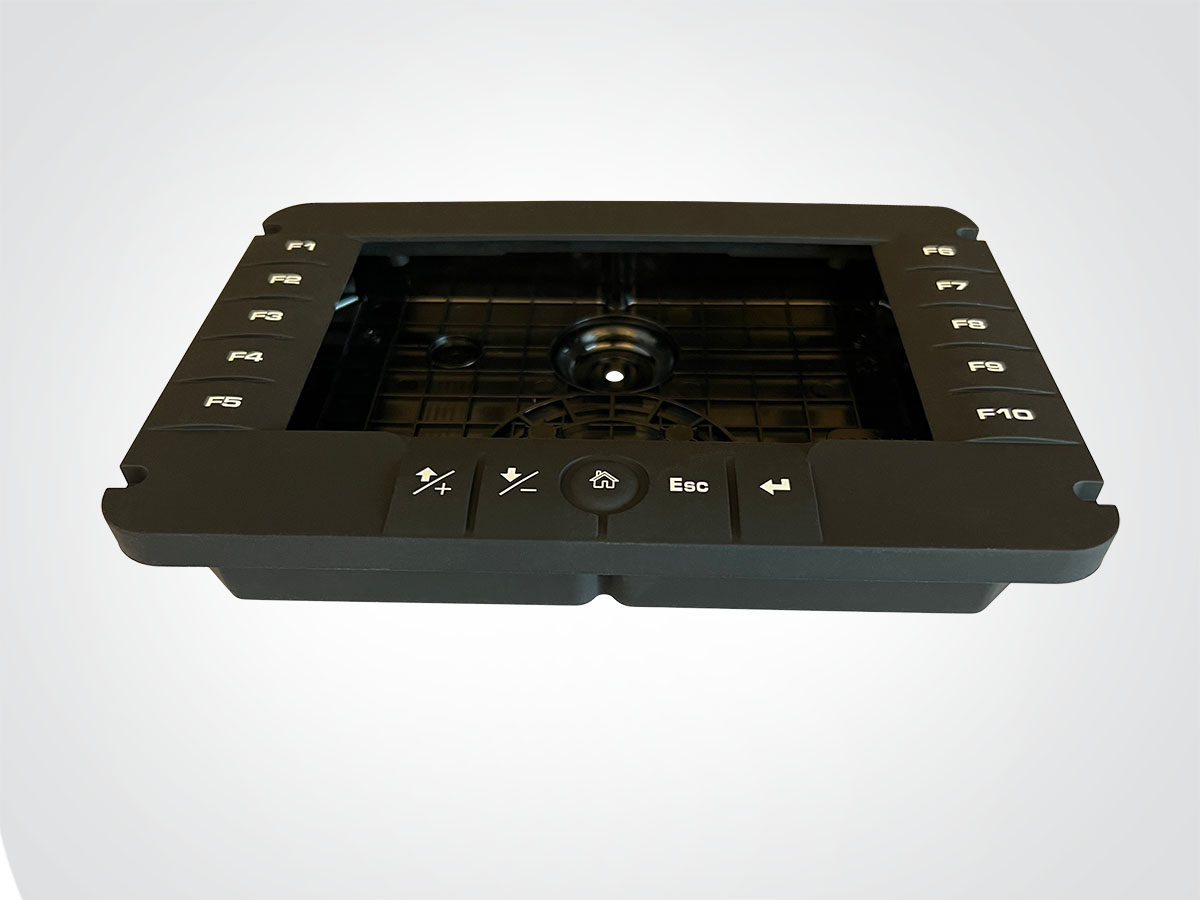
Co-moulding
Co-moulding is a combination of different moulded materials, which makes it possible to combine products into a single solution.
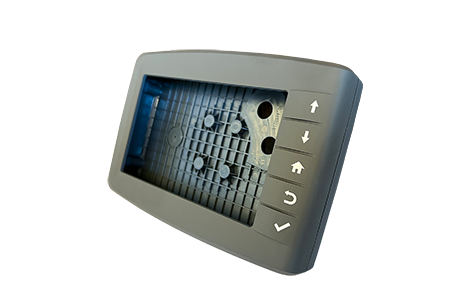
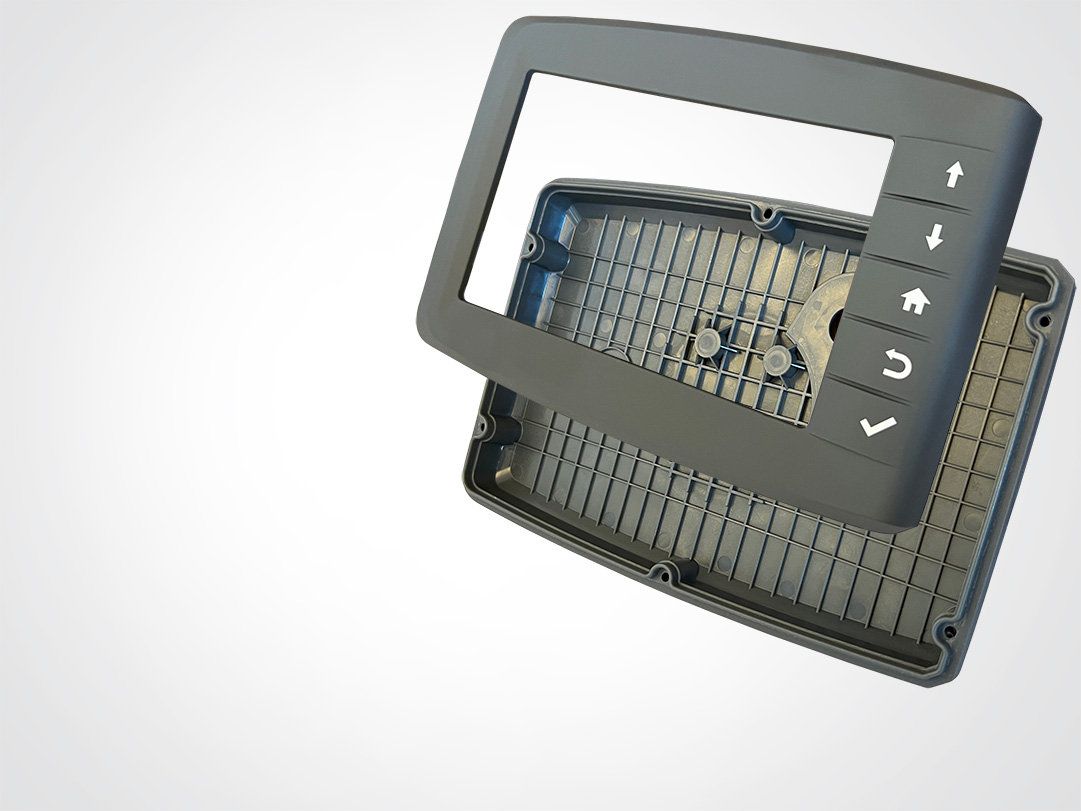
The benefits of co-moulding
Co-moulding creates value by combining the best elements from the cabinet and the coated material such as silicone. A combination with a case and silicone keys that create a complete device has never been easier.
Using this method, you create a product that gives an exclusive expression while increasing some features, such as density and surface durability. It can provide a soft exterior with a hard core, control panels or other box build solutions where this provides a firm grip.
In addition, co-moulding saves you assembly work because your products are delivered as a finished item. There are many advantages to products produced with co-moulding such as:
- Better performance: Co-moulding can combine the best properties of different types of plastic and silicone, such as strength, durability, flexibility, resilience, aesthetics and comfort.
- Increased density: By casting the surface directly on the case, it is possible to achieve increased tightness with the product.
- Higher user satisfaction: Co-moulding can create products that are more attractive, functional and user-friendly. With co-moulding, your products can be adapted to specific needs and preferences.
- Less assembly work: By having your products co-moulded, you will save time on assembly work as your products are made as a single unit. Co-moulding optimises your product and gives you a simple process
Co-moulding optimises your product and gives you a simple process
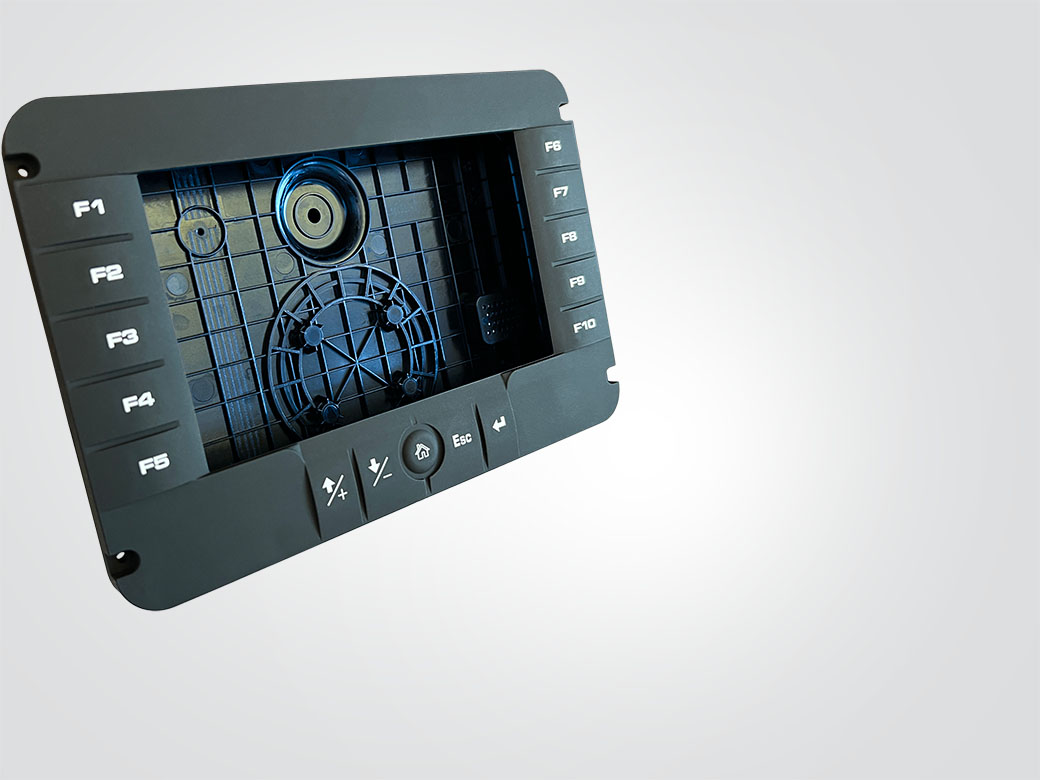
Co-moulding
Co-moulding is a combination of several materials that gives you a better and more complete product while simplifying assembly processes. This provides some unique options in terms of design and construction in combination with cabinets and control panels.
Co-moulding is done with an injection molding process to mold the enclosure. Then the outer layer, such as silicone, is molded directly onto the case. Thus, the keyboard and cabinets turn into one unit and benefit from both materials.
When two materials are combined in this way in one process, you can achieve high complexity, an improved design, optimized function and a shorter assembly process. The density increases and the durability becomes better, while the user experience of the product becomes unique.
Due to the many possibilities offered by the combinations of materials, co-moulding is a good choice for complete solutions. Space can be cast for electronic components, such as displays or PCBA, where it is delivered pre-assembled.
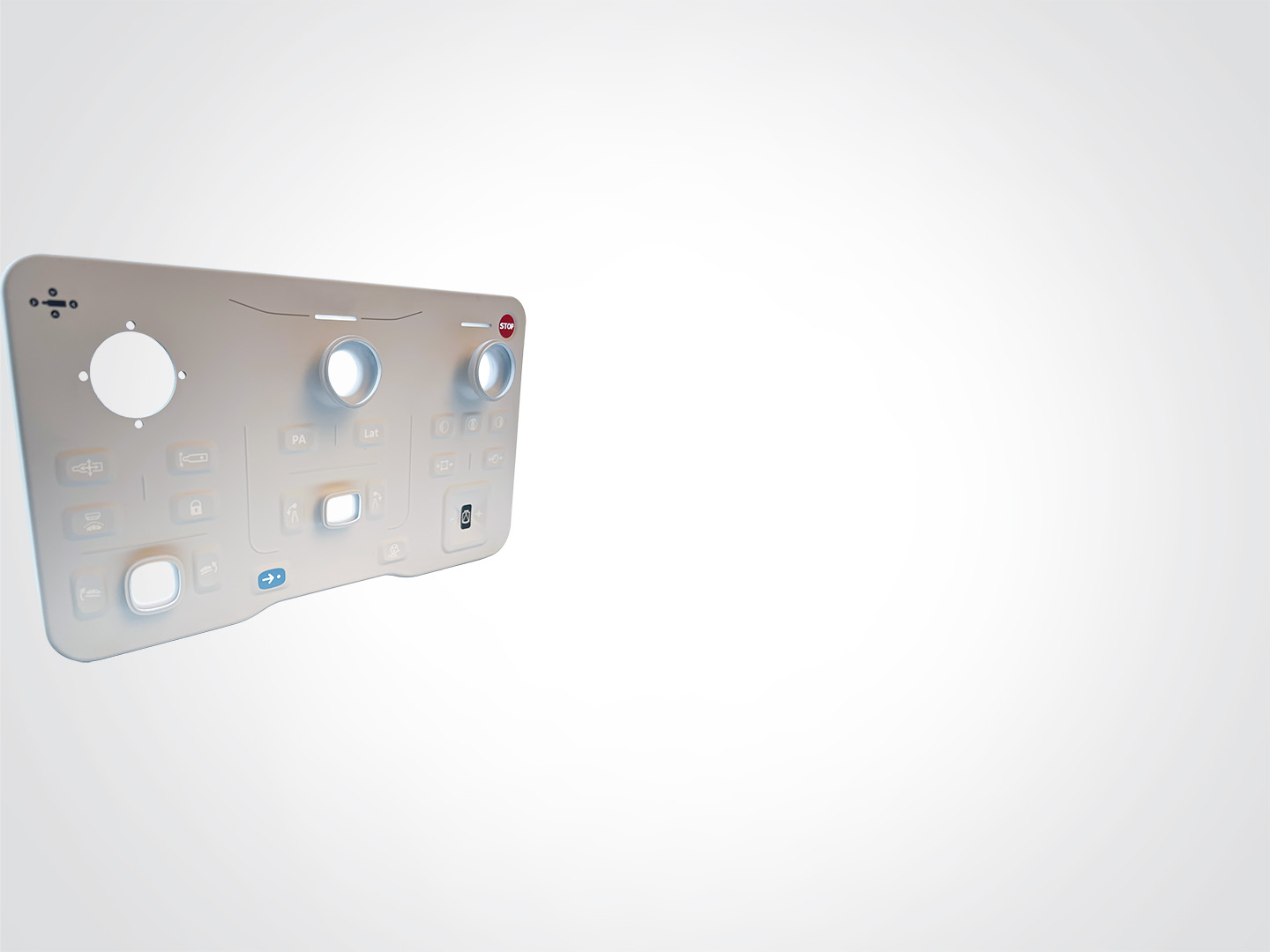
Integrated backlight
With a product made with co-moulding, you can easily integrate backlight and light into the keys or at areas that display information.
Backlight is integrated directly into the product using, for example, laser edge engraving or is printed so that the areas of information are illuminated. It can provide a practical function for products that are used in dark or poor lighting, or as an aesthetic design solution, as the light can help to give some nice effects.
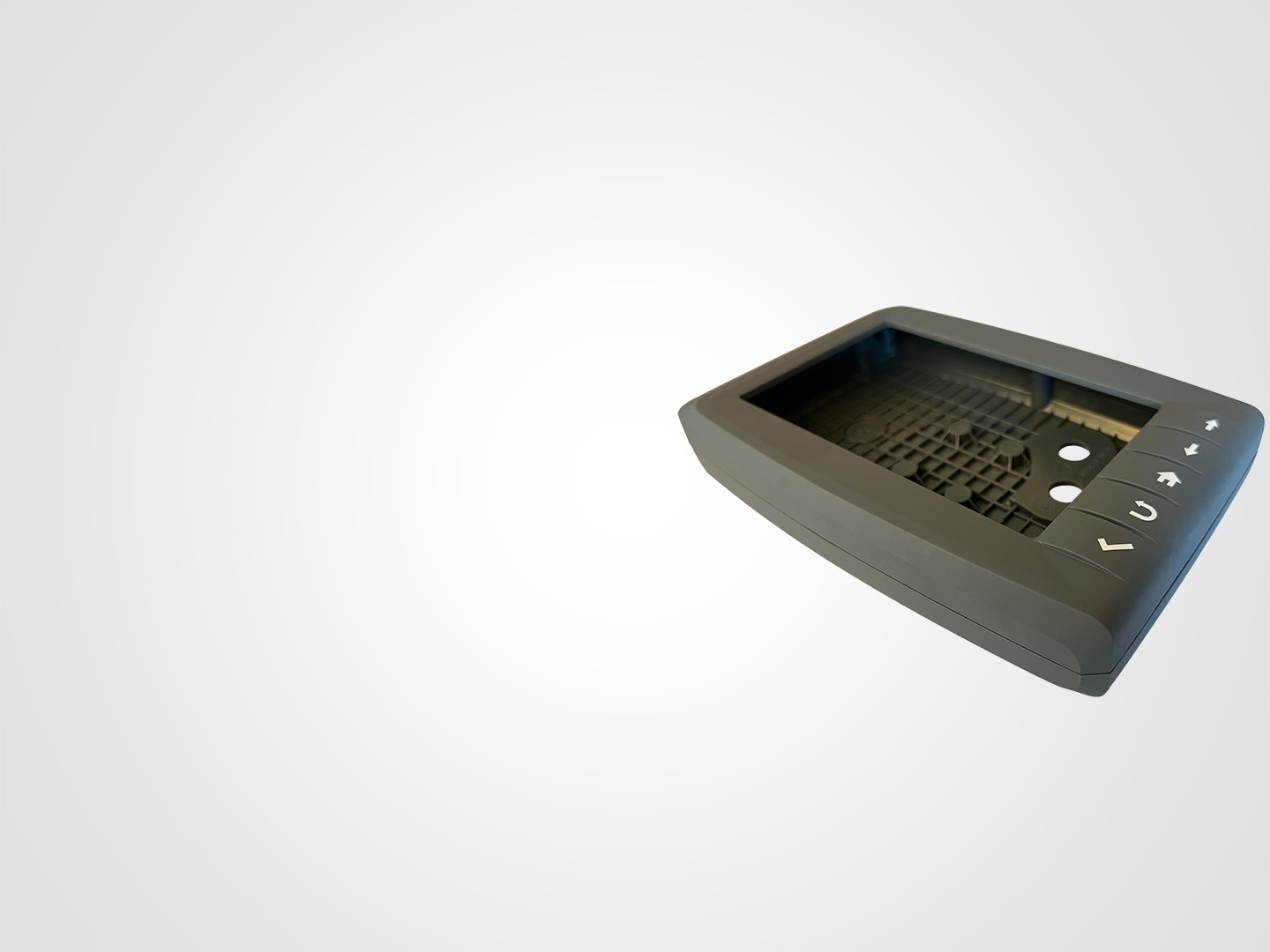
A finished product
By using co-moulding, you can advantageously assemble the entire product with all content, e.g. display, touchscreen, PCB or cables. The product will be molded to fit your electronic content. This gives the opportunity to gather everything in one place with the components to be mounted in the product.
For further information
%20(1)-1.png)
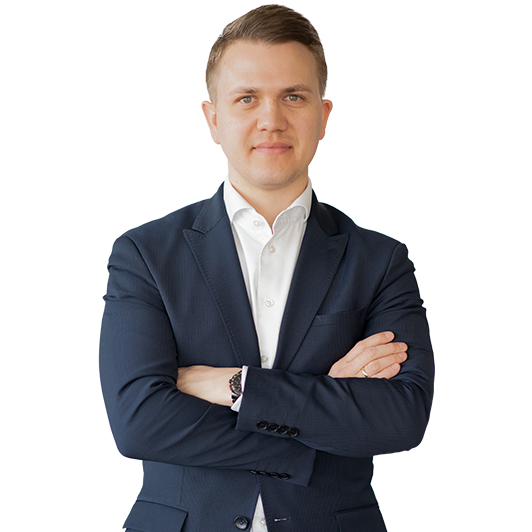